Mbsm.tn, Understanding Low Pressure and High Pressure in Refrigeration Systems
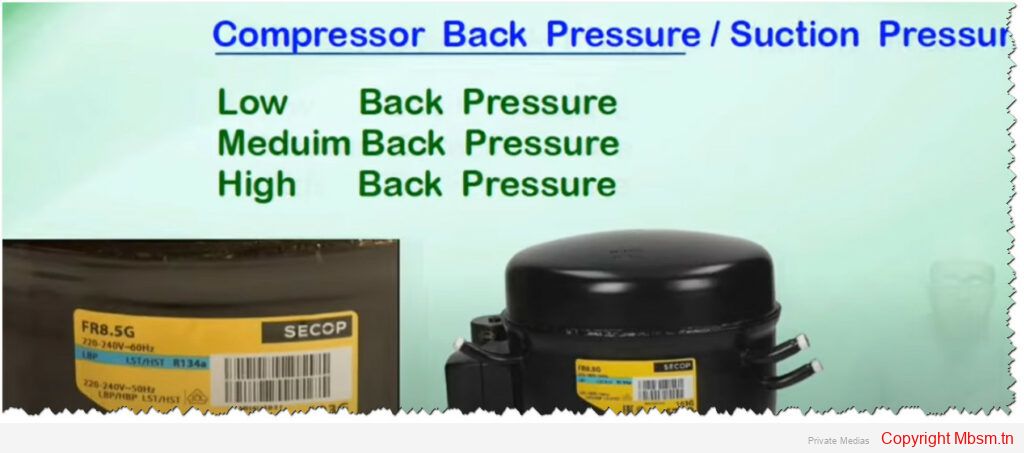
Understanding Low Pressure and High Pressure in Refrigeration Systems
Refrigeration systems operate on the principles of thermodynamics, utilizing refrigerants that change states between liquid and gas to absorb and release heat. The system is characterized by two distinct pressure zones: low pressure (or evaporating pressure) and high pressure (or condensing pressure). Understanding these pressures is crucial for the efficient operation of refrigeration systems.
Low Pressure (Evaporating Pressure)
The low-pressure side of a refrigeration system includes components such as the evaporator and the suction line leading to the compressor. Here, the refrigerant exists primarily as a low-pressure gas. The key processes involved are:
- Evaporation: The refrigerant absorbs heat from the environment (e.g., from inside a refrigerator) and evaporates, transitioning from a liquid to a gas. This process occurs at low pressure, which allows the refrigerant to absorb heat effectively at lower temperatures12.
- Pressure Measurement: The evaporating pressure can be measured using a gauge placed between the metering device outlet and the compressor. Accurate readings are essential for diagnosing system performance1.
The evaporating pressure is critical because it dictates how effectively the refrigerant can absorb heat. As pressure decreases, the saturation temperature also decreases, allowing for cooling at lower temperatures
5.
High Pressure (Condensing Pressure)
The high-pressure side encompasses components such as the compressor discharge, condenser, and discharge line. The processes here include:
- Compression: The compressor takes in low-pressure gas from the evaporator and compresses it into a high-pressure gas. This compression increases both the pressure and temperature of the refrigerant, preparing it for heat rejection in the condenser24.
- Condensation: In the condenser, the high-pressure gas releases its heat to the external environment and condenses back into a liquid state. This phase change occurs at high pressure, which is necessary for effective heat transfer15.
The condensing pressure is measured anywhere between the compressor’s discharge valve and the entrance to the metering device. Proper monitoring ensures that the system operates within safe limits to prevent failures or leaks
3.
Key Differences Between Low and High Pressure
Feature | Low Pressure (Evaporating) | High Pressure (Condensing) |
---|---|---|
State of Refrigerant | Primarily vapor | Primarily liquid |
Function | Absorbs heat | Releases heat |
Measurement Location | Between metering device and compressor | Between compressor discharge and metering device |
Pressure Range | Typically lower than atmospheric | Higher than atmospheric |
Temperature Relation | Lower saturation temperature | Higher saturation temperature |
Importance of Pressure Control
Maintaining appropriate pressure levels is vital for safe and efficient operation. Excessive pressures can lead to equipment failure or catastrophic events like refrigerant leaks or explosions
3. Therefore, components such as expansion valves or capillary tubes play critical roles in regulating these pressures by creating resistance to fluid flow, ensuring that refrigerants transition smoothly between high and low pressures throughout their cycle56.In summary, understanding low and high pressures in refrigeration systems is essential for their effective operation. These pressures dictate how refrigerants absorb and release heat, ultimately determining the efficiency of cooling systems.